Lean Six Sigma Consulting in California
Contact Us
Understanding the Lean Six Sigma Process
Simply stated, Lean Six Sigma Experts of California works on eliminating inconsistencies, inefficiencies in service, or errors while a company manufactures a service or fine. Lean Six Sigma usually employs a control map with points corresponding to the commodity production process. When translated to the points seen on the table, approved goods and procedures must fall into a particular category. Furthermore, points that do not fall under the defined limits are regarded as faults or defects in the system.
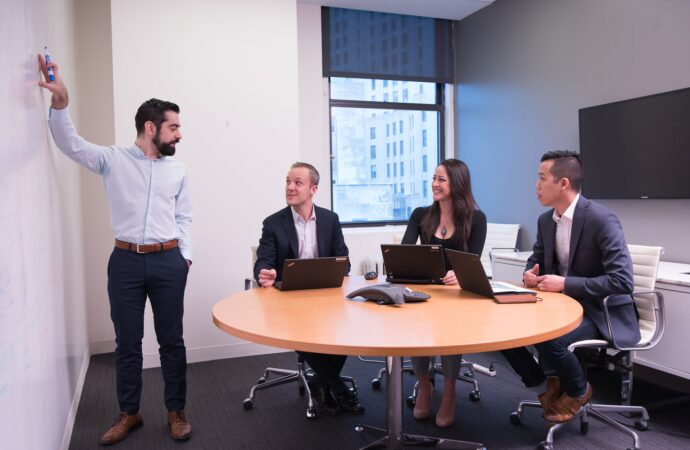
Reasons to use Lean Six Sigma Experts of California
Assists you in developing your business strategy: Lean Six Sigma Experts of California is critical to a company's corporate outlook. When the company determines its task, goals, and performs a SWOT review, the use of Six Sigma methods allows you to focus on areas for change in a more precise and effective manner. Let us use an illustration to demonstrate this. If the market plan is to become a cost leader, Lean Six Sigma will increase yields, improve internal procedures, retain the lowest cost supply deals, and eliminate unnecessary complications. Keeps the employers and staff motivated: What is the path to corporate growth that many founders and business owners fail to recognize? It is the efficiency of the employees and the workers. This helps in improved efficiency, which turns into higher service sales. However, for the workers to work and deliver consistently, they must be motivated and encouraged. Rapidly developing companies who retain their workers engaged to see a 25 to 50 percent rise in inefficiency. Using Six Sigma problem-solving methods and resources successfully fosters workforce growth and assists in the development of an organizational culture of positive knowledge-sharing and employee engagement. Helps you dramatically decrease cycle times: There are times that company ventures go over their deadlines. This is largely attributed to improvements made to the project scope and recent developments in management policies. When you use Six Sigma methods, you may form teams of expert experts at all levels of the company. Professionals are often recruited from all functional verticals. This unit is charged with determining the causes that could have a detrimental effect on the project leading to long periods. This team will then be asked to search for possible ways to minimize the detrimental consequences. Many prestigious brands that have implemented Six Sigma have recorded a 35% reduction in cycle times. Assists you in developing your business strategy
Keeps the employers and staff motivated
Helps you dramatically decrease cycle times
Since finding the correct Lean Six Sigma partner, as selecting every other partner, manufacturer, or provider, is vital to program progress, it seems only appropriate to extend expertise to designing a few often asked questions to consider while assessing prospective partners. Here are some of the more frequently asked questions, along with some insight into the types of responses to be expected:
What is your initial startup procedure with a new client?
A Lean Six Sigma collaborator can cooperate with you and key partners within the company to form a cross-functional implementation team. The associate you pick should be a specialist in education, methods, and best practices for implementation. The company members should have realistic expertise using any of the current process management methodologies to achieve sales outcomes, as well as an understanding of the organization’s overall business plan and consumer approach. If the first phase of the startup process is just about arranging training courses, this could raise a red flag. Any Lean Six Sigma implementation in an organization can begin with an understanding of the consumer strategy and existing change management and process transformation culture, followed by the creation of a plan that adapts the solution to those realities.
What are your project selection and project startup procedure?
When incorporating Lean Six Sigma into the company’s world, project selection is crucial. Breaking down strategic target areas into concept proposals is one of the main aspects of this process. The project procurement process can ensure that high-value, well-scoped initiatives are defined and connected to strategic goals, thus minimizing unnecessary project lead times and lack of internal organizational resources. Following the discovery of proposals, a dialogue with key stakeholders should take place to confirm tentative conclusions and prioritize projects.
Not only can several Lean Six Sigma ventures be found, but other initiatives that the organization can address will also be uncovered. The startup process for chosen Lean Six Sigma project proposals can provide project charters, which are written to include the business justification for each project and act as the steering structure for improvement efforts. It is also at this stage where baseline benchmarks are developed, enabling us to monitor the success of projects and process improvements.
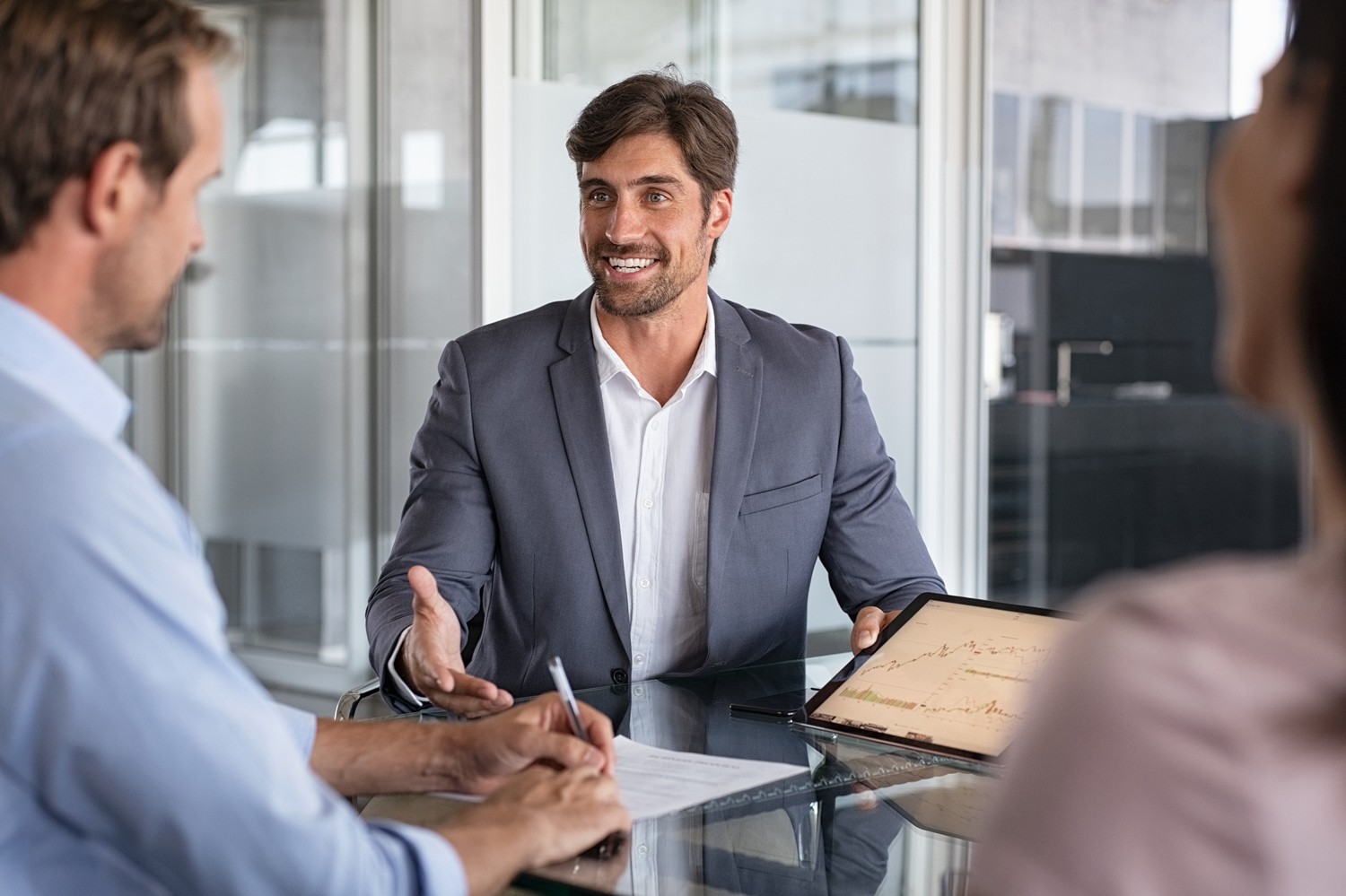
Is Lean Six Sigma a set of improvement initiatives?
The continuous implementation of the techniques overtime is needed. Each part of the team must be mindful of their duties and obligations. Every person must be evaluated critically about team goals. Similarly, in the company, Lean Six Sigma must be regarded as a long-term approach rather than a sequence of measures. It is all about improvement. The leadership’s dedication to the plan paves the way for the future. It is a question of tradition and approach rather than an undertaking.
It necessitates long-term dedication. The strategy must be reflected in the strategies and organizational framework. Present facts and statistics, and use them to evaluate results. Recognize behaviors that are consistent with modern culture. Reward outcomes achieved from the new approach.
How does it benefit the customer?
Many people have assured me, “We are a customer-driven company!” Sounds fine, but what separates customer-driven companies from conventional organizations? Customer-driven companies, on the other hand, are devoted to delivering high-quality goods and services that fulfill the expectations of their clients.
You step into a restaurant and order pizza. The amount you love the pizza is determined by what you wanted and what was delivered. When you get more than you expected, you are ecstatic. On the opposite, if there is a disparity in what you planned and what you got, it contributes to disappointment.
Lean Six Sigma Experts of California presents you with tools and a framework for defining what the consumer needs and, most specifically, measuring it. This eliminates doubt from discussions of “What Good Looks Like.”
How does it benefit employees?
If you know the “bad systems trigger 95% of errors”? In several organizations, therefore, errors are labeled as a “People Problem” or “Human Error.”
What is the ramification? They want to patch people while continuing through flawed systems.
The emphasis in a Lean Six Sigma setting is on production performance and lean processes. Efforts are being geared toward improving systems to minimize mistakes. Reduce human involvement in routine jobs by removing or automating them. As a result, the monotony of repeat work is eliminated, enabling workers to devote their resources to higher-value tasks.
Lean Six Sigma Experts of California also provides individuals with a plethora of ways to regularly practice different strategies. After implementing the same within their departments, they will be able to educate others on the strategies and implementation. This all contributes to continued professional growth.
There are so many areas or regions where we offer these services with most of them being cities.
However, if you need any of these services, you need to contact us. The list below comprises the areas where we offer these services.